The realm of electrical connections assumes a pivotal stance in ensuring the seamless operation of diverse apparatuses and systems, spanning from automobiles to household contrivances. In the realm of shielding these connections against the perils of dampness, corrosion, and sundry environmental agents, dielectric grease has stood as a favored option. However, circumstances may arise that beckon forth alternatives to the aforementioned grease. Within the confines of this composition, we shall embark on an exploration of optimal replacements for dielectric grease, unearthing their attendant merits, and delving into their efficacious utilization.
Why Consider Alternatives to Dielectric Grease?
Dielectric grease finds its foundation in a silicone-based compound, harnessed meticulously to insulate and safeguard electrical connections. Its prowess in fending off moisture and thwarting the advances of corrosion positions it as the preferred option for an array of scenarios, spanning the realms of automotive, maritime, and domestic applications. However, circumstances may arise wherein alternatives warrant consideration:
- Availability: Imagine being marooned in a land where dielectric grease is as elusive as a mirage. In such moments of urgency, having a substitute waiting in the wings can be nothing short of a knight in shining armor. Whether it’s a silicone-based lubricant or even a simple petroleum jelly, having a plan B can save the day when the spotlight falls on you;
- Cost: Dielectric grease, while a champion, can sometimes be a costly one. As the curtains rise on larger applications – sprawling automotive endeavors or maritime escapades – the expenses can pile up like discarded scripts backstage. Enter the thrifty understudy – a cost-effective alternative. With a judicious selection, your wallet might just deliver a standing ovation;
- Compatibility: In the grand tapestry of electrical connections, not all materials share a harmonious waltz with dielectric grease. When certain components turn a cold shoulder, you’ll want an alternative that’s the Fred Astaire of the electrical world – one that can lead with finesse, irrespective of the partner’s composition. It’s the compatibility tango, and a graceful alternative can ensure no toes are stepped on;
- Specific Properties: The theatrical production of electrical engineering occasionally demands a star with a unique skill set. Be it soaring temperatures that could turn lesser greases into puddles, or the need for heightened conductivity to conduct the symphony of electrons, the understudy alternative might be ready to steal the spotlight. These bespoke performers bring just the right notes to a specific scene.
Best Substitutes for Dielectric Grease
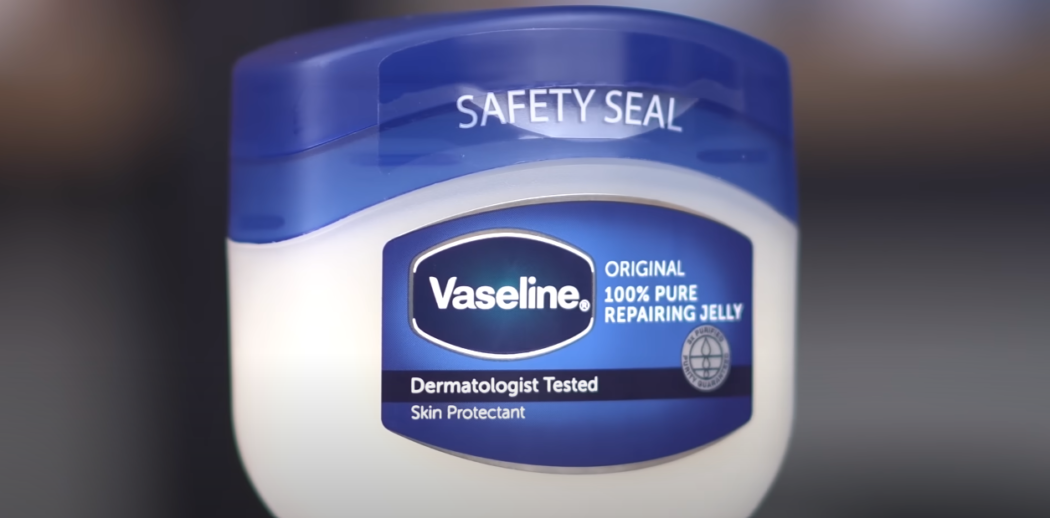
When it comes to ensuring the longevity and proper functioning of electrical components, dielectric grease plays a crucial role by providing insulation, protection against moisture, and prevention of corrosion. However, in cases where dielectric grease is not readily available or a different solution is sought, there are several alternatives that can be considered. Below, we delve into a detailed comparison of these substitutes, highlighting their advantages, disadvantages, and unique characteristics.
Vaseline (Petroleum Jelly)
Advantages | Disadvantages |
---|---|
Widely available | Lower temperature range |
Cost-effective | Can attract dust and dirt |
Good moisture barrier |
Vaseline, commonly known as petroleum jelly, presents itself as a versatile and cost-effective alternative to dielectric grease. Its widespread availability makes it convenient for various applications, while its ability to form a moisture barrier adds a layer of protection. However, Vaseline’s performance is limited by its lower temperature range, and over time, it may accumulate dust and dirt, potentially affecting its efficacy.
White Lithium Grease
Advantages | Disadvantages |
---|---|
Good water resistance | Can become runny at high temperatures |
Versatile | |
Higher temperature tolerance |
White Lithium Grease, typically employed as a lubricant, demonstrates its adaptability as an electrical insulator. Its robust water resistance and higher temperature tolerance compared to Vaseline make it a contender. However, it’s essential to note that under high temperatures, this grease can become runny, which might lead to messy situations.
Petroleum Jelly
Advantages | Disadvantages |
---|---|
Easily available | Limited temperature range |
Forms protective barrier | Potential rubber degradation |
Cost-effective |
Another readily accessible option, petroleum jelly, boasts its ability to create a protective barrier that shields against moisture and corrosion. While it’s budget-friendly, its temperature range is restricted, potentially making it unsuitable for extreme conditions. Furthermore, prolonged use of petroleum jelly on rubber components might contribute to their degradation.
Silicone Grease
Advantages | Disadvantages |
Wide temperature range | Relatively more expensive |
Excellent water resistance | |
Chemically stable |
Silicone grease emerges as a specialized alternative with a broad temperature range and exceptional water resistance. Its chemical stability ensures durability over time. However, the advanced properties come at a cost—silicone grease tends to be more expensive compared to other substitutes.
Coconut Oil
Advantages | Disadvantages |
Natural and biodegradable | Limited temperature range |
Good moisture resistance | Might become rancid over time |
For an environmentally conscious option, coconut oil presents itself as a natural and biodegradable alternative. Its ability to resist moisture is noteworthy. However, its usage is limited by temperature, and without regular application, it might turn rancid.
Using Alternatives Effectively
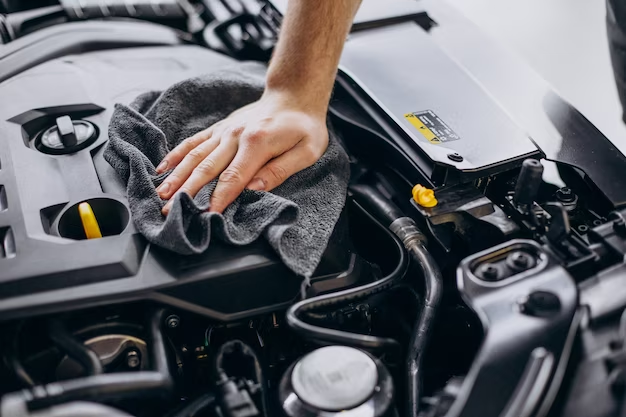
When it comes to maintaining the integrity of electrical connections and preventing corrosion, dielectric grease is a go-to solution. However, there are times when using alternatives becomes necessary. Whether you’re out of dielectric grease or seeking a unique solution, employing substitutes effectively requires finesse. Here’s your guide to making the most of alternatives, presented in a format that’s both informative and engaging.
1. Clean Surfaces for Optimal Performance
Picture this: a spark plug socket, a car’s ignition system, and a packet of alternative grease. Before diving in, the cardinal rule is ensuring pristine surfaces. Dirt, debris, and residual grease can hinder the performance of substitutes. Here’s where you can embrace the power of cleanliness:
Step | Description |
---|---|
1 | Inspect: Examine the connection points closely. Identify any debris or existing grease. |
2 | Cleanse: Use an appropriate cleaner or solvent to remove dirt and grease. Ensure surfaces are dry before applying alternatives. |
3 | Precision: Opt for tools like brushes, cotton swabs, or compressed air to meticulously clean crevices. |
2. Compatibility as the Cornerstone
Imagine a scenario: you’ve found an alternative grease, but what if it reacts adversely with the materials involved? Compatibility check is non-negotiable. In the world of alternatives, harmony between materials is key:
Factor | Guideline |
---|---|
Materials | Research: Understand the components of both the alternative and the application site. |
Reactions | Test Zone: Apply a small amount of the alternative in an inconspicuous area. Monitor any reactions before a full application. |
Longevity | Durability: Ensure that the alternative’s effectiveness isn’t compromised over time due to material interaction. |
3. Embracing the Temperature Spectrum
Visualize this: an industrial setting with machinery operating at elevated temperatures. Temperature resistance of an alternative is paramount. Different environments require different solutions:
Scenario | Guidance |
---|---|
High Temperatures | Selection: Choose an alternative with a temperature range that suits the environment. |
Low Temperatures | Cold Comfort: Similarly, ensure the substitute can withstand colder conditions without losing effectiveness. |
4. Precision in Quantity
Envision this: a delicate electronic circuit where precision is the name of the game. Overdoing it with the alternative can lead to problems. Applying the right amount is an art:
Step | Process |
---|---|
1 | Measure: Depending on the surface area, gauge how much alternative you’ll need. |
2 | Layering: Apply a thin, uniform layer of the substitute. It’s about protection, not excessive buildup. |
3 | Spot-on: Focus on areas that need it the most, ensuring that the coverage isn’t excessive. |
Conclusion
Dielectric grease remains a reliable choice for protecting electrical connections from moisture and corrosion. However, having alternatives on hand can be valuable in situations where dielectric grease is not available or not the best option. When considering substitutes, factors such as temperature range, moisture resistance, and compatibility should guide your choice. By following proper application techniques and guidelines, you can effectively safeguard your electrical connections and ensure their longevity.
FAQ
While cooking oils might offer some level of protection, they are not recommended substitutes. They have limited resistance to moisture and temperature fluctuations, which are essential for effective electrical insulation.
It’s generally not recommended to mix different substitutes unless you are certain of their compatibility. Mixing substances with unknown interactions could lead to unforeseen issues.
Yes, coconut oil is a natural alternative that offers some level of moisture resistance. However, it has limitations in terms of temperature range and shelf life.
Yes, many substitutes can be used in automotive applications where dielectric grease is typically used. Just ensure that the chosen substitute meets the required temperature and moisture resistance criteria.
The frequency of reapplication depends on factors such as environmental conditions and usage. Regular inspections should help you determine when reapplication is necessary.